Step-by-Step Guide to Preventing Weld Undercut in Different Metals
Step-by-Step Guide to Preventing Weld Undercut in Different Metals
Blog Article
Grasping the Art of Welding: Exactly How to Prevent Undercut Welding Issues for Flawless Manufacture Outcomes
Performance and precision are extremely important worldwide of welding, where also the slightest imperfection can endanger the architectural stability of a produced piece. One common challenge that welders face is undercutting, a defect that can compromise a weld joint and lead to pricey rework. By comprehending the origin causes of undercut welding and carrying out reliable strategies to stop it, welders can boost their craft to new levels of excellence (Preventing weld undercut). In the quest of perfect manufacture outcomes, mastering the art of welding to avoid undercut problems is not simply an ability yet a need for those pursuing excellence in their work.
Understanding Undercut Welding
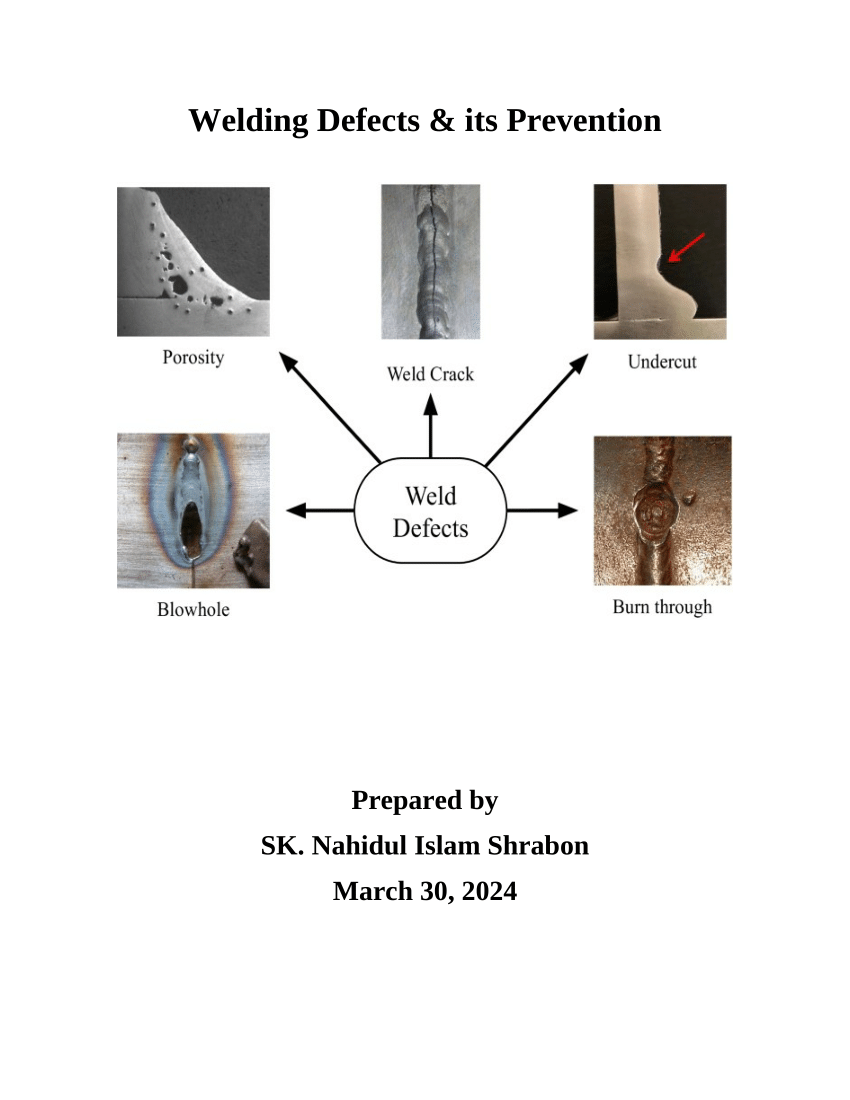
To protect against undercut welding, welders need to ensure proper welding parameters, such as changing the present, voltage, travel speed, and keeping the correct electrode angle. By recognizing the causes of undercut welding and executing precautionary actions, welders can accomplish top quality, structurally audio welds.
Causes of Undercut in Welding
Recognizing the elements that contribute to damage in welding is necessary for welders to generate top notch, structurally sound welds. Inadequate welding present or inaccurate welding rate can additionally contribute to undercut. Understanding these causes and executing proper welding methods can aid avoid damaging concerns, guaranteeing strong and long lasting welds.
Methods to stop Undercutting

To minimize the risk of damaging in welding, welders can employ tactical welding methods aimed at boosting the top quality and stability of the weld joints. Furthermore, making use of the correct welding method for the details joint arrangement, such as weave or stringer beads, can add to lowering damaging.
Additionally, appropriate joint prep work, including making certain clean base materials without pollutants and making use of the suitable welding consumables, is important in stopping undercut flaws. Utilizing back-step welding methods and regulating the weld grain profile can likewise aid distribute warmth uniformly and minimize the threat of undercut. Routine examination of the weld joint during and after welding, as well as executing top quality assurance procedures, can help in detecting and resolving damaging problems promptly. By executing these methods diligently, welders can achieve flawless manufacture results with marginal undercut defects.
Relevance of Proper Welding Parameters
Selecting and maintaining appropriate welding specifications is necessary for achieving effective welds with marginal issues. Welding specifications refer to variables such as voltage, present, take a Read Full Report trip speed, like this electrode angle, and protecting gas flow rate that directly affect the welding procedure. These parameters have to be thoroughly adjusted based upon the type of material being welded, its density, and the welding technique utilized.
Correct welding parameters ensure the appropriate quantity of warmth is applied to thaw the base steels and filler product uniformly. If the criteria are established also high, it can bring about excessive warmth input, creating spatter, burn-through, or distortion. On the various other hand, if the parameters are too reduced, incomplete combination, absence of penetration, or damaging might take place.
Top Quality Guarantee in Welding Workflow
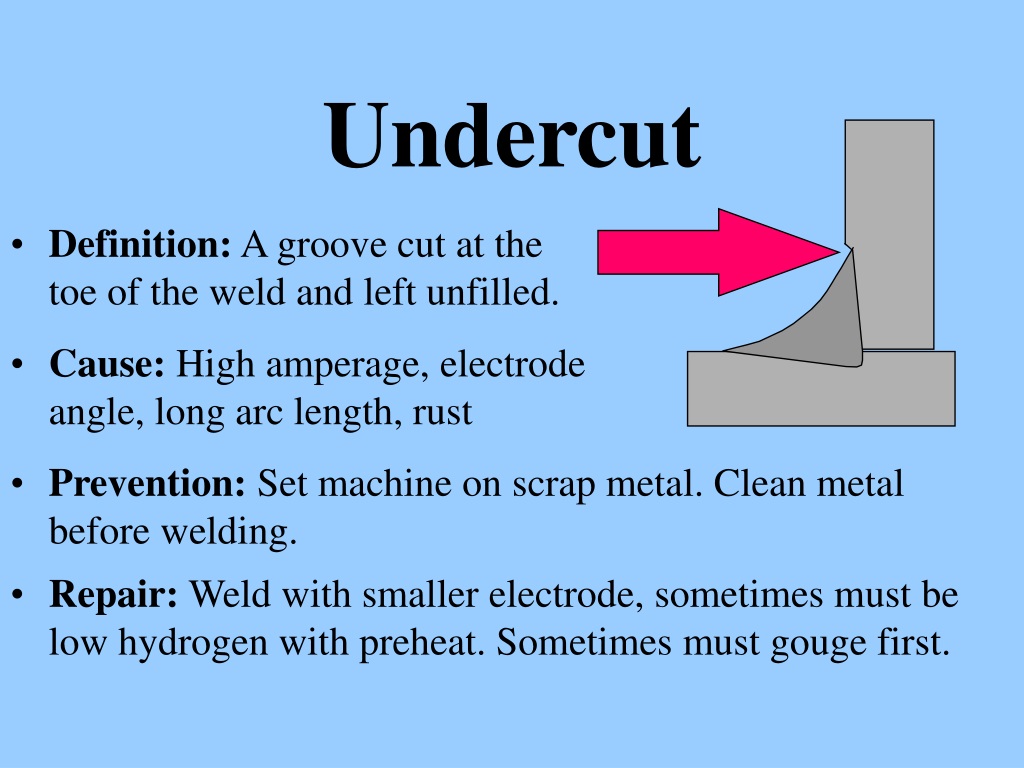
Conclusion
Finally, mastering the art of welding requires a thorough understanding of undercut welding, its reasons, and strategies to stop it. By making certain appropriate welding criteria and applying top quality guarantee techniques, flawless manufacture outcomes can be achieved. It is vital for welders to constantly aim for excellence in their welding procedures to avoid undercut problems and produce high-quality welds.
Undercut welding, a common defect in welding procedures, takes place when the weld steel does not properly fill the groove and leaves a groove or depression along the welded joint.To prevent undercut welding, welders need to ensure correct welding specifications, such as readjusting the current, voltage, traveling rate, and keeping the appropriate electrode angle. Poor welding wrong or existing welding rate can likewise contribute to undercut.To minimize the threat of undercutting in welding, welders can utilize calculated welding strategies intended at enhancing the top quality and integrity of the weld joints.In verdict, grasping the art of welding needs an extensive understanding of undercut welding, its causes, and techniques to prevent it.
Report this page